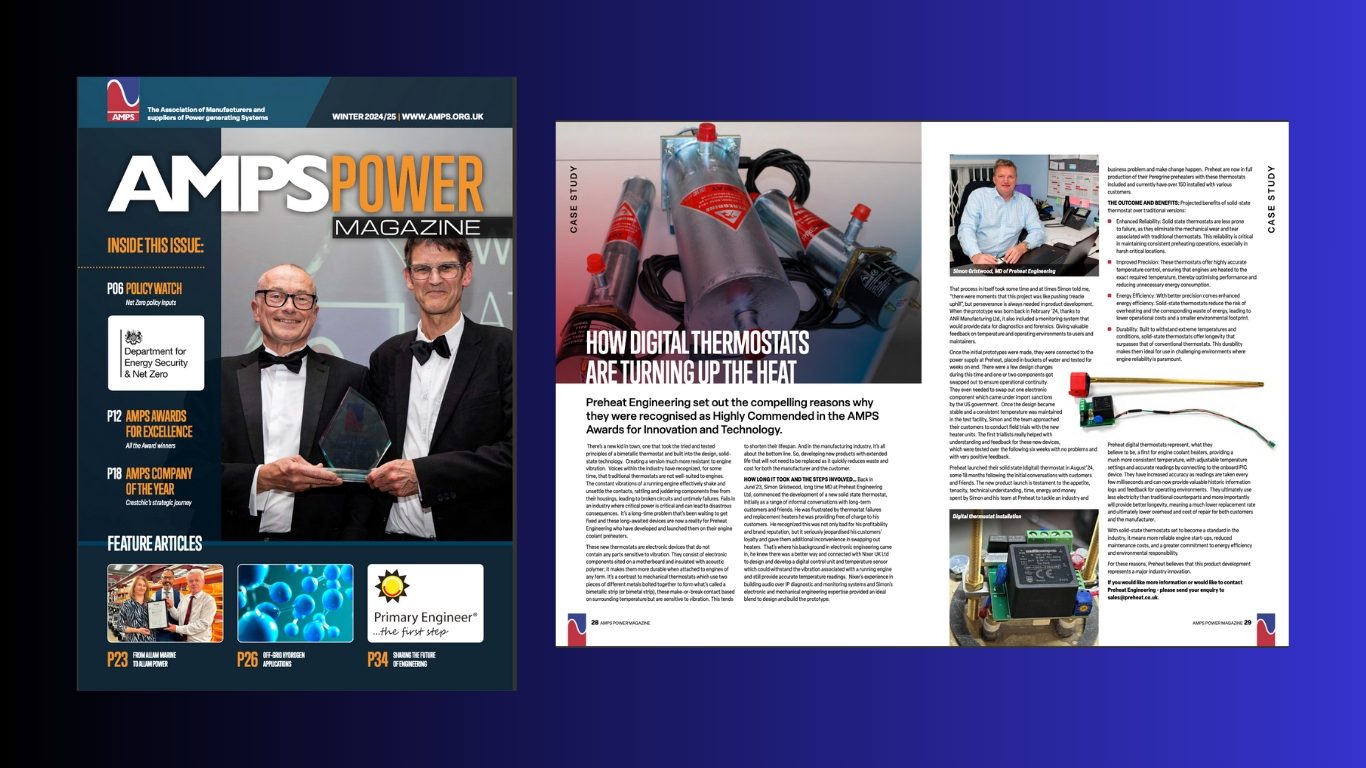
The AMPS Power Magazine is packed full of AMPS and industry news.
AMPS Power is the voice of the UK’s Power Gen sector.
The Winter issue features Preheat Engineering being recognised in the case study section.
Preheat Engineering set out the compelling reasons why they were recognised as Highly Commended in the AMPS Awards for Innovation and Technology.
There’s a new kid in town, one that took the tried and tested principles of a bimetallic thermostat and built into the design. solid-state technology. Creating a version much more resistant to engine vibration. Voices within the industry have recognised, for some time, that traditional thermostats are not well-suited to engines.
The constant vibrations of a running engine effectively shake and unsettle the contacts, rattling and juddering components free from their housings, leading to broken circuits and untimely failures. Fails in an industry where critical power is critical and can lead to disastrous consequences. It’s a long-time problem that’s been waiting to get fixed and these long-awaited devices are now a reality for Preheat Engineering who have developed and launched them on their engine coolant preheaters.
These new thermostats are electronic devices that do not contain any parts sensitive to vibration. They consist of electronic components sited on a motherboard and insulated with acoustic polymer; it makes them more durable when attached to engines of any form. It’s a contrast to mechanical thermostats which use two pieces of different metals bolted together to form what’s called a bimetallic strip (or bimetal strip), these make-or-break contact based on surrounding temperature but are sensitive to vibration. This tends to shorten their lifespan. And in the manufacturing industry, it’s all about the bottom line. So, developing new products with extended life that will not need to be replaced as it quickly reduces waste and cost for both the manufacturer and the customer.
HOW LONG IT TOOK AND THE STEPS INVOLVED…
Back in June 23, Simon Gristwood, long time MD at Preheat Engineering Ltd, commenced the development of a new solid state thermostat, initially as a range of informal conversations with long-term customers and friends. He was frustrated by thermostat failures and replacement heaters he was providing free of charge to his customers. He recognised this was not only bad for his profitability and brand reputation, but it seriously jeopardised his customers’ loyalty and gave them additional inconvenience in swapping out heaters. That’s where his background in electronic engineering came in, he knew there was a better way and connected with Nixer UK Ltd to design and develop a digital control unit and temperature sensor which could withstand the vibration associated with a running engine and still provide accurate temperature readings. Nixer’s experience in building audio over IP diagnostic and monitoring systems and Simon’s electronic and mechanical engineering expertise provided an ideal blend to design and build the prototype.
That process in itself took some time and at times Simon told me, “there were moments that this project was like pushing treacle uphill”, but perseverance is always needed in product development.
When the prototype was born back in February’24. thanks to ANR Manufacturing Ltd, it also included a monitoring system that would provide data for diagnostics and forensics. Giving valuable feedback on temperature and operating environments to users and maintainers.
Once the initial prototypes were made, they were connected to the power supply at Preheat, placed in buckets of water and tested for weeks on end. There were a few design changes during this time and one or two components got swapped out to ensure operational continuity.
They even needed to swap out one electronic component which came under import sanctions by the US government. Once the design became stable and a consistent temperature was maintained in the test facility, Simon and the team approached their customers to conduct field trials with the new heater units. The first trail-lists really helped with understanding and feedback for these new devices, which were tested over the following six weeks with no problems and with very positive feedback.
Preheat launched their solid state (digital) thermostat in August’24, some 18 months following the initial conversations with customers and friends. The new product launch is testament to the appetite, tenacity, technical understanding, time, energy and money spent by Simon and his team at Preheat to tackle an industry and business problem and make change happen. Preheat are now in full production of their Peregrine preheaters with these thermostats included and currently have over 150 installed with various customers.
THE OUTCOME AND BENEFITS: Projected benefits of solid-state thermostat over traditional versions:
Enhanced Reliability: Solid state thermostats are less prone to failure, as they eliminate the mechanical wear and tear associated with traditional thermostats. This reliability is critical in maintaining consistent preheating operations, especially in harsh critical locations.
Improved Precision: These thermostats offer highly accurate temperature control, ensuring that engines are heated to the exact required temperature, thereby optimising performance and reducing unnecessary energy consumption.
Energy Efficiency: With better precision comes enhanced energy efficiency. Solid-state thermostats reduce the risk of overheating and the corresponding waste of energy, leading to lower operational costs and a smaller environmental footprint.
Durability: Built to withstand extreme temperatures and conditions, solid-state thermostats offer longevity that surpasses that of conventional thermostats. This durability makes them ideal for use in challenging environments where engine reliability is paramount.
Preheat digital thermostats represent, what they believe to be, a first for engine coolant heaters, providing a much more consistent temperature, with adjustable temperature settings and accurate readings by connecting to the onboard PIC device. They have increased accuracy as readings are taken every few milliseconds and can now provide valuable historic information logs and feedback for operatina environments. They ultimatelv use less electricity than traditional counterparts and more importantly will provide better longevity, meaning a much lower replacement rate and ultimately lower overhead and cost of repair for both customers and the manufacturer.
With solid-state thermostats set to become a standard in the industry, it means more reliable engine start-ups, reduced maintenance costs, and a greater commitment to energy efficiency and environmental responsibility.
For these reasons, Preheat believes that this product development represents a major industry innovation.
If you would like more information or would like to contact Preheat Engineering – please send your enquiry to
sales@preheat.co.uk
WE ARE HERE TO HELP YOU FIND THE PERFECT HEATING SOLUTION FOR YOUR NEEDS.